See This Amazing Log Home With Rustic Interior
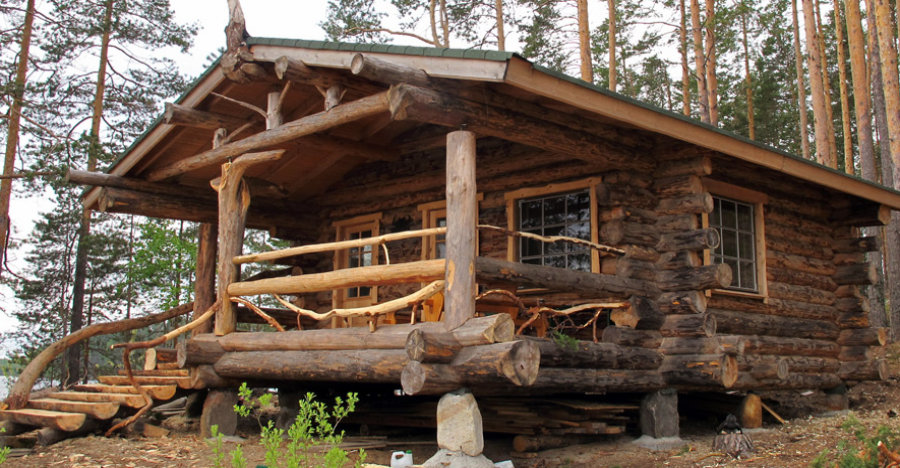
The Vatisaari hideaway was carved directly from the storm-pine pines on the construction site.
The building has a natural stone base, the corner type is a dense and beautiful saddle corner, the diameter of the logs is 40 to 25 cm, and the headboards and window sills are made of sheathed sawn spruce. A root hook was saved at the end of the cuckoo log and a rhizome decoration on the terrace pole. The sauna benches were also carved from massive roots. Shop Tiny Homes Exterior finishing with tar. Aarre magazine, Lansi-Savo, and the future of the country published stories about the Vatisaari log. house construction project. This log cabin is beautifully crafted inside and out from the hand-carved logs and the unique log railings. The following are just some of the details of the build.
Traditional Hand-Carving Conditions.
Log house construction has not changed significantly in the last hundreds of years. New handy tools and inventions have made it possible to work more and more accurately. Thanks to the effective dissemination of knowledge, hundreds of years of experience, and research work, log house construction is of higher quality today than ever before. The traditional log construction method has been tested and developed for a thousand years, with good results. Log houses built hundreds of years ago are still lived in today. The hand-built log house is made to last from one generation to the next.
Hand Carving.
The main principle of hand carving and the difference from industrial log house construction is that the trees are selected, arranged, and carved as individuals. The heights of the logs vary and the trees preserve natural forms from the bases, tops, and nodules, which are carefully matched by a skilled sculptor. So the logs do not go through the planer or lathe and do not have glue joints. The last handcrafted finish is created with a soap iron and a chisel with which to finish the wall surfaces.
Stages of Log House Construction.
The quality of log house construction starts in the forest. Straight, slow-growing, dense, healthy-branched Redwood is probably the best wood in the world for a log cabin building. The logs are selected from the forest one by one according to the procurement list. After felling, the trees are transported to the building site and raw barked to allow the tree to dry. The final flow is created with hand tools in the sculpting phase. The result is a smooth, beautiful, and weather-resistant sculpture surface. After debarking, the trees are carefully tapped and left to dry. The logs should be dried for at least half a year to minimize cracking due to shrinkage.
In connection with debarking, the diameters of the trees are measured at the base and top, and other observations such as running, and more are recorded.
When the frame is finally sculpted, a suitable log for the wall is selected from the table. The shape of the lower wood is drawn with millimeter precision on the wood to be carved. The actual sculpture work is done with the help of a chainsaw and numerous hand tools (chute ax, concealer, chisels).
Photo Gallery
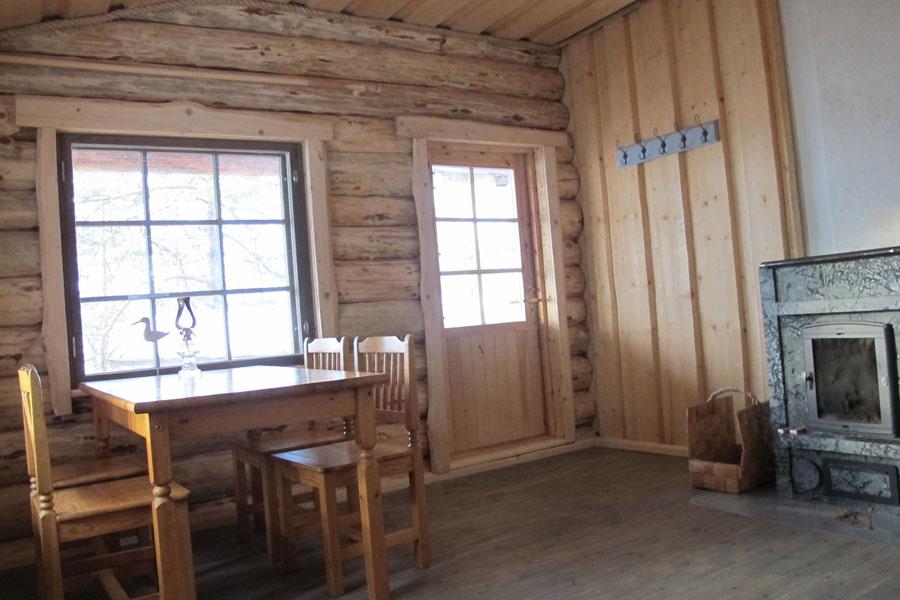